Application of thermal insulation materials in architectural coatings
Yang Jing, Wang Dongnan, Zhu Ming
(Sanshu Paint Co., Ltd., Putian, Fujian 351100)
Abstract: According to the different heat transfer modes of thermal insulation materials, they are divided into barrier-type thermal insulation materials, reflective thermal insulation materials and radiation-type thermal insulation materials. The application of the above three types of thermal insulation materials in architectural coatings is summarized, and their advantages and disadvantages are analyzed and summarized. The development trend of various architectural coating thermal insulation materials is prospected.
Key words: thermal insulation materials; architectural coatings; application
0 Preface
With the development of social economy and the improvement of people's living standards, the global demand for energy is increasing, and the problem of energy shortage is becoming more and more prominent. According to statistics, the proportion of building energy consumption in human energy consumption is generally around 30%, and most of it comes from air conditioning heating and cooling. Therefore, reducing building energy consumption is of great significance. At present, the measures used to reduce building energy consumption in the market mainly use building insulation mortar and EPS external insulation system, but the above two traditional building materials all have flammable, easy to crack and leak, easy to fall off and other defects. As a new type of green and environmentally-friendly building energy-saving materials, building thermal insulation coatings have obvious advantages and broad market development prospects. Building thermal insulation coatings rely on thermal insulation materials for their thermal insulation. Therefore, it is the direction of many researchers to seek new building insulation materials and modify them to improve insulation efficiency.
1· Barrier type thermal insulation material
Barrier insulation is a type of material that slows down the heat transfer process.
The barrier type thermal insulation coating is applied to the surface of the wall to form a thermal insulation layer having a certain thickness. Assuming that the coating is uniform, the temperatures on both sides of the coating are t1 and t2, respectively, and t1>t2, the coating thickness is b, and the coating layer is coated. The area is S, as shown in Figure 1, the heat conduction process can be ideally considered to be a stable one-dimensional flat-wall heat conduction. The heat transfer equation obtained by Fourier's law is shown in formula (1):
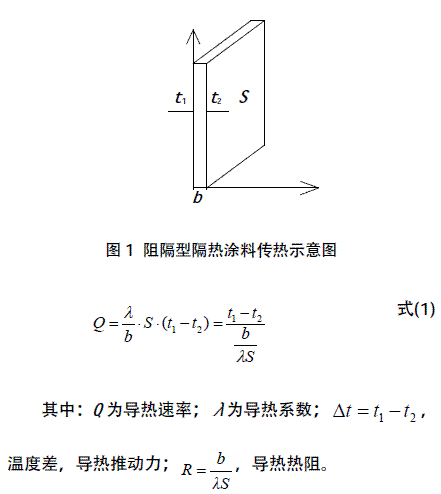
It can be known from formula (1) that in order to make the thermal conductivity lower, the thermal resistance R is required to be larger, that is, the barrier type thermal insulation coating is required to have two characteristics: one is that the thermal conductivity λ is small, and the other is the dry film thickness after construction b. Larger.
The thermal conductivity of the barrier type thermal insulation coating is achieved by adding a barrier type thermal insulation material with a lower thermal conductivity. Therefore, the thermal conductivity is an important indicator for screening barrier type thermal insulation materials, and common barrier type thermal insulation materials. Materials include: sepiolite, expanded perlite, expanded vermiculite, palygorskite, calcium silicate, diatomaceous earth, asbestos, slag wool, hollow glass microbeads, hollow ceramic microbeads, etc., some barrier insulation materials at room temperature The thermal conductivity underneath is shown in Table 1.
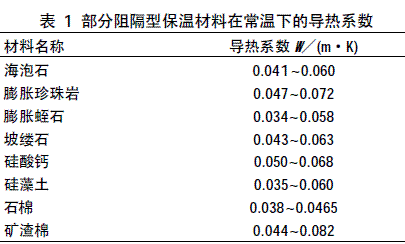
Among them, sepiolite, palygorskite, asbestos, rock wool, slag cotton belong to inorganic fiber type minerals, inorganic fiber can increase the viscosity of the slurry and improve the crack resistance of the coating, but the amount added in the paint should not be too large, otherwise It is easy to cause the coating viscosity to be too high to be applied, the appearance of the coating film is rough and unequal, and many inorganic fiber minerals are carcinogenic. The lower cost composite silicate thermal insulation material has developed rapidly in China, and it is mainly used as industrial thermal insulation coatings, such as high temperature pipeline insulation, or insulation of boilers, kiln furnaces, etc. The expanded vermiculite is darker in color and has a greater influence on the hue of the paint after it is added. Hollow glass microspheres and hollow ceramic microbeads have low thermal conductivity due to the encapsulation of air with low thermal conductivity, and they have high reflectivity to sunlight, so they are also a reflective thermal insulation material, but in the coating. The amount of addition should not be too large, generally 5%~10% (mass fraction), otherwise the coating viscosity is too high, the heat storage stability is poor, the appearance of the coating film is rough and the cracking risk of the paint film is high, and the stain resistance is high. Poor performance and other issues.
In order to exert the excellent thermal insulation effect of the barrier type thermal insulation material, the coating should have a large thermal resistance.

To reduce the thermal conductivity.
In addition, it should have a certain thickness. Therefore, the barrier type thermal insulation coating is a thick film coating, and the coating thickness is generally 5 to 20 mm. However, the thicker paint film has the disadvantages of long drying period and high risk of cracking, and the barrier type heat insulating material is a lightweight material with a large porosity, which also brings a problem of poor impact resistance to the paint film. Therefore, the application of barrier type thermal insulation materials in architectural coatings is still limited.
2. Reflective thermal insulation materials
Reflective thermal insulation materials are a class of materials that have a high reflectivity for sunlight. In sunlight, about 95% of the energy is concentrated in the visible and infrared regions. In this wavelength range, the higher the reflectivity of the reflective insulating material, the better the thermal insulation effect.
Reflective thermal insulation materials used in the early days are highly reflective metal or metal oxide pigments and fillers, and are often used in solvent-based systems because of their poor stability in aqueous systems. Moreover, the thermal conductivity of metal and metal oxides is generally high, and the thermal conductivity is good, which is unfavorable for heat insulation. At present, the widely used reflective heat insulating materials are hollow microsphere materials with low thermal conductivity and good stability in an aqueous medium, such as hollow glass microbeads, hollow ceramic microbeads, and expandable microspheres. A large amount of research work is mainly concentrated on two aspects: one is the screening of different kinds of hollow microsphere materials and the optimization of the dosage and the ratio of different sizes; the other is the other components in the coating formulation (such as the type of emulsion, the amount of titanium dioxide, and the help). The choice of agent and the choice of PVC, etc., balance the negative impact of the addition of hollow microspheres on the performance of the coating, and through adjustment to ensure the optimization of thermal insulation performance. Wang Xiaxia et al. orthogonally designed the amount of filler and hollow glass microspheres used in the formulation, and determined that the optimum mass ratio between titanium dioxide, hollow glass microbeads, mica powder and kaolin was 6:2:2:2.5:1.5. A good insulation effect has been achieved. Wang Xiaoli et al. selected emulsions for reflective thermal insulation coatings, using pure acrylic emulsions and silicone-acrylic emulsions with a mass ratio of 2:1 as film-forming materials, and achieved in terms of elasticity, strength, stain resistance and thermal insulation properties. balance.
Reflective thermal insulation materials provide thermal insulation by reflecting solar radiant heat, and the ability to reflect solar radiant heat depends on the color, chemical composition and surface flatness and smoothness of the surface of the material, especially the surface color affects the reflectivity. The main factor. The lighter the surface, the stronger the ability to reflect solar radiant heat. For example, the white surface has a reflectivity of more than 0.7 for solar radiation, and the black surface has a reflectance of only 0.1. The current literature reports focus on the application of reflective thermal insulation materials in light-colored architectural coatings, and have achieved certain results, while the development of dark solar thermal reflective coatings is more difficult. Li Yunde used hollow glass microbeads as thermal insulation materials to study the heat reflection performance of several single color paint systems. It was found that the higher the brightness, the higher the solar reflectance, and the addition of hollow glass beads can improve the 酞. The infrared band reflectance of the cyan pigment system increases the solar reflectance, but the increase is not large. Sun Yuanbao et al. studied the thermal insulation properties of green solar heat reflective coatings using conventional reflective thermal insulation materials such as titanium dioxide, barium sulfate and far-infrared ceramic powder. It was found that the key is the choice of pigments, especially black pigments. Compared with ordinary green paints, the green solar heat reflective paint can reduce the surface temperature by up to 10 °C, and its cooling effect is very obvious. Naofusa Yamada found that commonly used black pigments such as carbon black, iron black, and copper chrome black have high infrared absorption rates, while matte blacks composed of red and cyan or yellow and violet reduce infrared absorption in the 380-780 nm range, so Reflective insulation with lower infrared absorption can be obtained by blending dark colors with a single color to achieve a lower infrared absorption reflective insulation, which provides a solution for dark architectural coatings.
Due to the high solar reflectivity of reflective heat-insulating materials, reflective heat-insulating coatings can usually be made into thin-coated products, which overcomes the shortcomings of long-term drying cycle and high risk of cracking of barrier-type thermal insulation coatings. In recent years, reflective thermal insulation coatings have been flourishing, and reflective thermal insulation materials have also become the research object of many experts and scholars. The research on reflective thermal insulation materials has also achieved certain results. Because architectural coatings have decorative effects, especially for building exterior wall coatings, white or light colors are less used. Therefore, how to make reflective insulation materials play a role in dark architectural coatings is the research of reflective thermal insulation coatings. One of the hot spots.
3. Radiant thermal insulation materials
Radiant thermal insulation materials are a class of materials with high thermal emissivity, which can emit heat to the air at a certain wavelength to achieve thermal insulation. Radiant insulation is more efficient than barrier and reflective insulation. Radiation-type thermal insulation coatings have only been developed in the last 10 years and are still in their infancy in China. At present, most of the infrared radiation materials used are far-infrared radiation ceramic powders. The commonly used materials are shown in Table 2.
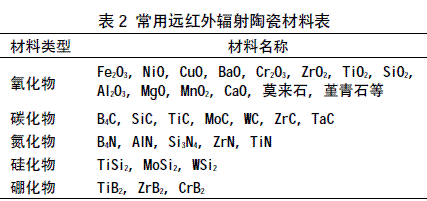
Far-infrared ceramic powders (such as MgO-Al2O3-TiO2-ZrO2, etc.) mixed with one or several oxides in the IIIth or Vth cycle of the periodic table have higher spectral emissivity at lower temperatures , is an ideal radiation material. Far-infrared ceramic powders composed of a mixture of two or more compounds sometimes have a higher specific emissivity than a single substance, so far-infrared radiation ceramic powders usually use a variety of inorganic metals and non-metal oxides, nitrides, and carbonization. The material, boride, silicide and or specific natural ore (such as mullite, cordierite) are mixed and ground in different proportions, and then calcined, ground and sieved at a temperature of 1 200~1 600 °C. It can radiate far infrared rays of a specific wavelength.
The application of far-infrared ceramics (powder) can be divided into two aspects: the application of the medium-high temperature zone and the application of the normal temperature zone. Normal temperature infrared ceramic powder can radiate far infrared rays with a wavelength of 3~5 μm near room temperature (20~50 °C), which is more suitable for building thermal insulation coatings. At present, the contribution of far-infrared ceramic powder to thermal insulation and its effect on coating performance are under study.
4· Other insulation materials
The vacuum state can completely eliminate the molecular vibration heat conduction and convection heat conduction. Therefore, the use of vacuum materials to prepare thermal insulation coatings with excellent performance has become one of the hot research topics. The US House Laboratory has achieved good thermal insulation effect on the use of vacuum ceramic microbeads for civil buildings.
Phase change energy storage technology is an important technical measure for building energy conservation. Phase change materials (PCMs) and traditional building materials can be combined into a new building phase change energy storage material with heat storage and temperature regulation. . At present, the application of phase change materials in the field of building energy conservation is mainly to inject PCMs into wallboard, concrete blocks and PCMs for floor heating. The application in architectural coatings is still under study. With the increasing emphasis on green building materials and low-carbon environmental protection issues, phase change energy storage building materials have broad application prospects.
5 Conclusion
The application of domestic thermal insulation materials in architectural coatings mainly uses reflective ceramic materials such as hollow ceramic microbeads, hollow glass microspheres, and expandable microspheres, and has achieved phased results in the application of light-colored architectural coatings. The development of reflective insulation materials in colored and dark architectural coatings has become one of the new hot spots. Barrier-type thermal insulation materials are generally used in thick coatings to achieve their thermal insulation, while thick coatings do not have a competitive advantage compared to thin coatings, and how to seek more efficient (ie, lower thermal conductivity) The barrier type thermal insulation material is still one of the research focuses of many scholars and experts. Radiant insulation materials are widely praised by the industry. Radiation insulation materials are more efficient than barrier and reflective insulation materials, but their application in architectural coatings remains to be seen. In-depth study.
references
Huang Jian. Discussion on energy-saving technology of building engineering in China. Building Materials and Decoration, 2007, (12): 39-41.
Wang Kelin, Xu Na. Solar heat reflective thermal insulation coating and its development trend. Modern Coatings and Coatings, 2009, 12 (2): 19.
Wu Guojian, Jin Jun, Cai Yubin. Research Status and Development Trend of Thermal Insulation Coatings. Building Energy Conservation, 2011, 39(4): 56-58.
Lu Guozhong. Development of Building Reflective Thermal Insulation Coatings. China Coatings, 2007, 22(9): 37-40.
Xu Feng, Jiang Ziping. Research on Thermal Insulation Performance of Building Reflective Thermal Insulation Coatings. Shanghai Coatings, 2011, 49(6): 42-46.
Wang Xiaxia, Wang Qunying, Xiong Junshan, et al. Development of exterior wall reflective thermal insulation coatings. Coatings Industry, 2011, 41(3): 49-52.
Wang Xiaoli, Dong Zhou, Yang Sheng. Comparative Study on Formulation of Reflective Thermal Insulation Coatings, Coatings Industry, 2010, 40(7): 76-79.
Guo Nianhua, Chen Xian, Zhang Qiang, et al. Polyurethane modified high chlorinated polyethylene heat reflective coatings. Coatings Industry, 1999, 29(7): 11-13.
Li Yunde. Analysis of Standards and Main Technical Points of Solar Heat Reflective Coatings. Coating Technology and Abstracts, 2011, (6): 20-26.
Sun Yuanbao, Qiu Yuhui, Du Zhanshe, et al. Research on cooling performance of green solar heat reflective coatings. Electroplating and Finishing, 2006, 25(2): 22-25.
NAOFUSA YAMADA, HATSUO INAGAIKI, HIRo nOBU KAWASAKI.Solar
Heat-shieldingcoating composition and coated structure, US:
5540998.1996-07-30.
Ren Xiaohui, Zhang Xudong, He Wen, et al. Research progress and application of infrared radiation materials. Modern Ceramic Technology, 2007 (2): 26.
Liu Weiliang, Chen Yunxia. Preparation technology and properties of nanometer far infrared ceramic powder. Chinese Ceramics, 2002, 18 (1): 12-14.
Zhang Zhiqiang, Li Li, Liu Xiaoying, et al. Preparation and properties of phase change energy storage ceramsite. Wall Materials Innovation and Building Energy Efficiency, 2010(6): 33-35.
(Finish)
GF20/GF20CNC/GF25CNC Automatic Rebar Stirrup Bending Machine can bend round steel bar with diameter to various geometrics shape as required by construction.
Main Features Of Rebar stirrup bending machine
1. Convenient use: perfect safety performance, standard angle, fast speed, light and
handy.
2. Easy Operation: one man can operate it once switch on the power.
3. Convenient of range adjustment: for GF20 model, just need to shift induced magnet.
for GF20 CNC and GF25CNC model, just need to press the button on operation panel
4. We adopt two foot pedals: 90°and 135°, angle adjustment freely.
5. Fast Speed: rotate speed is 20-25 times/min (GF20), 25-30 times/min(GF25).
Cnc Rebar Stirrup Bending Machine
Cnc Rebar Stirrup Bending Machine,Cnc Stirrup Rebar Bending Machine,Automatic Cnc Stirrup Rebar Bending Machine,New Mechanical Rebar Bending Machine
BAODING JINDI MACHINERY CO., LTD , https://www.rebarconnector.com