The use of adhesives and sealing materials in petrochemical machinery not only has technically outstanding advantages over other conventional fastening methods, but also has significant economic benefits, which are mainly manifested in: improved product quality. The petrochemical machinery products bonded with adhesives and sealing materials are light in weight, with uniform stress distribution at the bonding sites and smooth and smooth appearance.
It can save materials and increase production efficiency. For example, a light machine produced by a US oil machinery company, with adhesive instead of riveting, can save 763 rivets per machine. Russia has statistics, the use of 1t adhesive can save 4 5t of metal or 1. 8t of metal fasteners, and directly saved manpower is equivalent to saving 6000 ~ 11000 US dollars of expenditure.
Can meet special needs. Such as the use of sealant can eliminate the leakage of petrochemical machinery products (oil leakage, leakage and leakage), the leakage of the factory high-pressure pipeline, can not stop for pressure plugging.
The defective products can be rejuvenated, damaged oil components can be repaired and put back into use. The impregnated glue is used to impregnate the sand holes and pores of the castings, so that the waste defective castings can be renewed. In the fracture, deformation, wear cracks, and leak repair of gears, spindles, valves, etc., a large number of adhesive technologies have been used to protect equipment from being scrapped.
Polymer bonding and sealing materials are mainly used for maintenance, sealing and plugging in the petrochemical machinery industry. There are various types of petrochemical machinery products. Common requirements for bonding and sealing materials include: in addition to good shear strength and tensile strength, sufficient toughness, impact resistance, fatigue resistance, and creep resistance are required. And can withstand repeated vibrations.
Good resistance to aging, resistance to media and environmental adaptability.
Satisfy the temperature requirements, the expansion coefficient is small, and it will not produce too much internal stress due to temperature changes.
Curing time is short, curing temperature is low, rapid solidification of adhesive at room temperature is conducive to energy saving and saving man-hours, especially in the case of salvage, more rapid curing at room temperature.
Insulation and isolation, eliminate galvanic corrosion factors.
Bonding and sealing materials commonly used in the petrochemical industry Bonding and sealing materials commonly used in petrochemical machinery, according to their main purposes, can be divided into five categories.
Universal adhesive: It is characterized by its ability to cure at room temperature, good overall performance, easy to use, suitable for bonding a variety of metal and non-metallic materials, commonly used in the bonding of small and complex parts, process positioning and mechanical repair. Mainly epoxy adhesives, there are a small amount of phenolic resins, polyvinyl alcohol adhesives.
Structural adhesives: Used for bonding of stressed components, able to withstand large loads. In the structural adhesives, epoxy resins and phenolic aldehydes and dicyandiamides dominated, but the long-term trend has declined, polyurethanes have grown faster, and acrylics have also developed faster.
Non-structural adhesive: It is mainly used for soft materials with low bonding strength, low strength but strong adhesion, and low elastic modulus. The main types are natural and synthetic rubber glues, emulsion glues, synthetic resin-modified synthetic rubbers, polyurethane glues and organic silica gels.
Pressure-sensitive adhesive and adhesive tape: It is a material that can be pasted under slight pressure at room temperature, does not dry for a long time, and maintains a certain adhesive force. It is mainly used for the paste of the nameplate, the symbol label, the protection of the surface of the precision instrument and the packaging of the components.
Application 1. Application in the maintenance of petrochemical machinery In the maintenance of petrochemical machinery, there are mainly repair adhesives and anaerobic adhesives.
There are many types of repair adhesive repair adhesives, including metal-filled adhesives, wear-resistant repair adhesives, corrosion-resistant repair adhesives, and emergency repair adhesives. According to its chemical composition, there are epoxy, polysulfone-dicyandiamide, butyl cyanide, phenolic, polysulfide and so on. Mainly used in adhesive repair of machinery and equipment.
For example, if the machine tool rails are worn out, they can be directly filled and repaired by the adhesive, and can be scraped into a flat bottom or a pointed bottom ditch to remove the oil stains. The glue is applied to the grooves, slightly above the work surface, and is to be flattened after curing. You can. Epoxy resin adhesives can be used: E-44 epoxy 100 parts, 650 polyamide 100 parts, 10 parts of dibutyl phthalate; Diethylaminopropylamine 7 parts, reduced iron powder 1 (1) to 200 parts.
Large engine block cracks can be found in the cylinder crack at one slot, the other processing a gutter washer, with adhesive to the gutter on the reinforcement, while blocking the cracks with an adhesive, can be put into use after curing.
Cavitation erosion, erosion and corrosion are the world problems faced during the use and maintenance of equipment. Petrochemical equipment corrosion is particularly serious. Some industrialized countries have investigated the damage caused by corrosion, and the corrosion loss accounts for 2% to 4% of the total national economic income. Surface-adhesive and preservative polymer adhesive materials have become one of the major anti-corrosion measures in petrochemical industry. Equipment maintenance plays an important role.
Anaerobic adhesive anaerobic adhesive is a widely used polymer adhesive in the field of mechanical maintenance. Anaerobic adhesive was invented by American Loctite in 1953. After many years of improvement and development, it is widely used in the bonding, fixing, locking and sealing of petrochemical machinery and other industrial machinery. China's anaerobic adhesive began its development in the 1960s and has developed more than a dozen brands.
Anaerobic adhesives are one-component adhesives, and their grades have different viscosities, such as dilute water and thick toothpaste. No reaction occurs in the air and it can be stored at room temperature. Once oxygen is insulative, polymerization will occur and cure quickly, so it is called "anaerobic adhesive". The main component of anaerobic adhesive is bisacrylic or dimethacrylic compounds.
Under the action of peroxide initiators and accelerators, it can be cured by free radical polymerization. However, when in contact with air, oxygen has a blocking effect on free radicals, cannot initiate polymerization, and can be safely stored in the air. Thickeners, thixotropic agents, and plasticizers are also often added to adjust viscosity and storage. The main uses of anaerobic adhesive are as follows: It is used for tightening and loosening of screw parts in various petrochemical machinery equipment. With anaerobic adhesive on the thread, when the internal pressure is isolated from the air, it can form a strong adhesive layer between the threads, playing an excellent locking and sealing effect. Experiments have shown that the anaerobic adhesive is 10 times more resistant to vibration and loose than spring washers and flat washers.
For sealing pipe threads and fittings. 60% of anaerobic adhesives abroad are used for sealing and locking. After the anaerobic adhesive for pipeline sealing is cured, the pressure resistance is up to 70 MPa. The bearing bushes, structural parts and process positioning are fixed.
2 Application in petrochemical machinery seals Mechanical joints Liquid gaskets are an important application of polymer seal materials in petrochemical machinery. Liquid gaskets, also known as liquid sealants, liquid gaskets, are made of resin and rubber base materials. At room temperature, it is a fluid viscous liquid that is applied to the joint surface of metal equipment and dried for 3 to 7 minutes to form a uniform, continuous and stable peelable elastic film or viscous, viscoelastic film. Most liquid gaskets are not cured. They are applied between the metal joints and clamped by bolts to prevent oil, water, gas, organic solvents, and acids and alkalis from leaking. At the same time, they are resistant to certain pressures and temperatures. It is non-corrosive and can replace asbestos rubber, copper and rubber gaskets for sealing against leakage. It can also be used with solid gaskets. Liquid gaskets have a significant effect on improving the tightness of mechanical equipment and preventing the leakage of oil and other liquid media. Commonly used domestic liquid gaskets are: W-1 type sealant, solvent-free type, do not have to dry directly after brushing, good detachability, mainly used for various pipelines, instrumentation, joints and thread parts. Applicable temperature: An anchor 609 sealant, strong adhesion to the components, easy to film elasticity, vibration resistance, water resistance and oil, the use of temperature up to 250 C, pressure 1MPa, can be used for grade or larger clearance Equipment, but it is difficult to disassemble and is suitable for parts that are not frequently disassembled.
3. Application of Plugging in Petrochemical Machinery Plugging technology mainly includes static plugging and pressure plugging. Plugging with pressure is an important application of polymer sealing materials in petrochemicals. The plugging technology with pressure refers to the process of the normal working of the system, such as the failure of the sealing structure, the leakage of equipment and pipelines, and the use of special means to achieve the sealing process without stopping the machine.
During the implementation process, the entire system maintains the normal circulation of the working medium under temperature and pressure, so this technology is difficult to implement.
The basic principle of pressure sealing and plugging technology is: the use of appropriate methods to form a short leak-free medium in the leakage area of ​​the use of adhesive wide applicability, good fluidity, fast curing and other characteristics, established in the leak The solid sealing structure composed of adhesive and various sealing materials achieves the purpose of stopping leakage.
Plugging with pressure is the first application in China and has developed into a practical new technology with Chinese characteristics such as caulking, top pressure bonding, fastening bonding, drainage bonding, magnetic pressure bonding and other methods.
Adhesives are the key to pressure plugging technology. The selection of adhesives for plugging is mainly based on the nature of the medium encountered during plugging, temperature, working pressure, and the material of the pipe and the degree of bonding surface treatment.
In general, the adhesive used for pressure plugging is selected in the existing adhesives, and special ones can be specially formulated. In the preparation process, the adhesive for plugging is more appropriate than that of general adhesives; the more reactive type is used. Adhesives; The volatility should be small; The curing time should be moderate, ensure sufficient operation time, and consider the use of inorganic adhesives for high temperature media.
Most of the raw materials for polymer bonding and sealing materials are used in the petrochemical industry and are also used in the petrochemical industry. In the field of petrochemical machinery, the application range of China's polymer adhesive sealing materials is still relatively narrow, and the application ratio is relatively small. In most cases, mechanical methods are still used. With the further development of China's polymer industry, polymer bonding and sealing materials will have considerable progress, and will be more widely used in the field of petrochemical machinery.
The information of professional knotted prairie cattle Field Fence
Material |
Galvanized iron wire, High tensile steel wire |
Inner wire diameter |
1.8-2.5mm |
Edge wire diameter |
1.9-3.5mm |
Surface treatment |
Electro galvanized, Hot dipped galvanized |
Height |
0.8m,1.0m, 1.2m, 1.5m,1.7m, 2.0m, 2.3m,2.6m |
Length |
10-200m |
Applications |
Used for borders in field and grassland for breeding of sheep, cattle,etc |
Characteristics |
Corrosion resistance, high tensile strength wire,firm structure,etc |
Packing |
Packed by plastic film, in carton box, in wooden pallet, in bulk. |
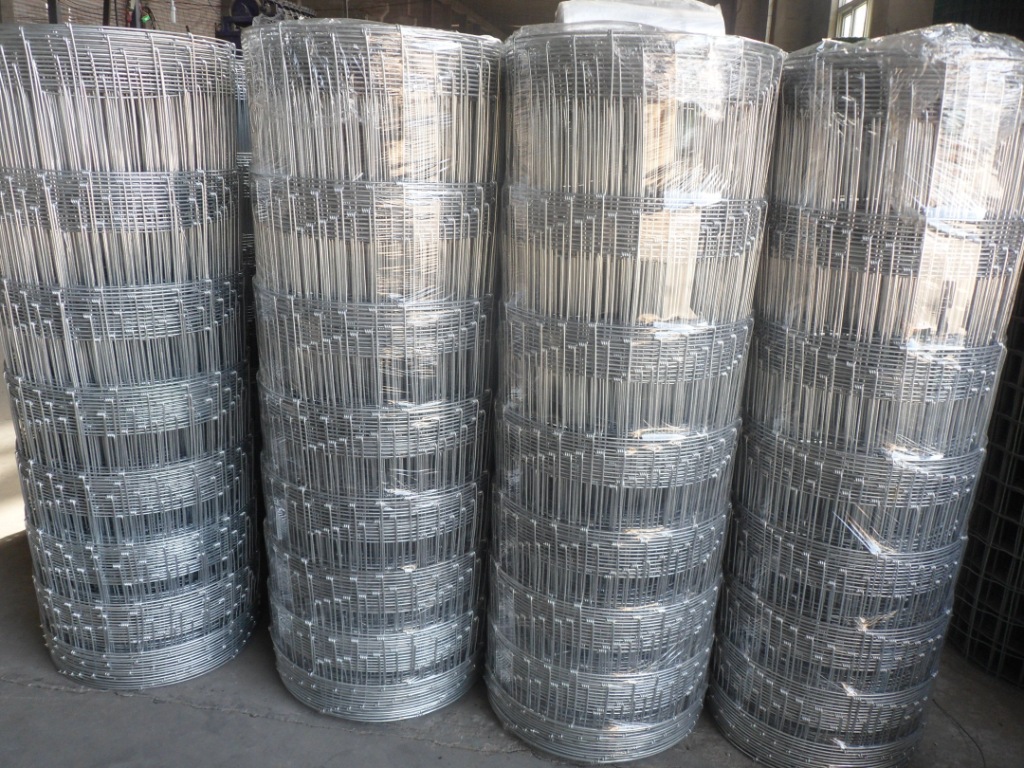
1.Material:
hot-dipped galvanized wire, which is made of Q235 iron rod.2.Anti-corrosion form:
hot-dipped galvanized and electric galvanized.
3.Application:
Field fence is a kind of mesh used in cattle, goat, deer, and pig. It is used for grassland, pastures,
protection of ecological projects, protecting grassland, forestry, highway, and environments
Field fence
Field Fence,Field Fencing,High Tensile Fence,Farm Fence
Anping Shengjia Hardware Mesh Co.,LTD , https://www.oilshaleshakerscreen.com